Identification of Potential Migrants into Food Simulants from Polyethylene Terephthalate Packaging

Full title of this study: "Identification of potential migrants into food simulants from commercially-manufactured, thermoformed virgin and post-consumer polyethylene terephthalate packaging."

Introduction
Food packaging is considered an indirect food additive according to the Code of Federal Regulations; therefore, risk assessment requires an understanding of packaging-component toxicities and predicted levels of human exposure [1-4]. Although the initial composition of the packaging may be known, the final composition can vary depending on physical and chemical degradation during the packaging’s life cycle prior to consumption of the product; this leads to recycling feed-stocks with large variations in composition [4]. The suitability of a recycled material for direct food contact therefore strongly depends on the source of the waste, and the recycling method [5, 6].
Migration of contaminants from packaging can adversely affect food quality giving it off-odors and flavors, and the contaminants may be toxic to consumers [4, 7, 8]. The degree of migration of a polymer component into food will depend on its initial concentration, mobility through the polymer matrix, duration of exposure at a particular temperature, and solubility of the component in the food [4, 8, 9].
Glass, steel, aluminum, and paper are commonly recycled for food contact applications. Contamination of these materials, except paper, due to consumer use and post-consumer handling is generally very low and the conditions of the recycling processes reduce contaminant concentration [5]. The Food and Drug Administration (FDA) categorizes recycling as: primary recycling -- the use of pre-consumer industrial waste to form a new product; secondary recycling -- the physical reprocessing and reformation of post-consumer materials; and, tertiary recycling -- the chemical treatment of post-consumer materials to isolate components to be reprocessed [5]. A majority of the post-consumer reprocessing done in the United States is secondary recycling. Secondary recycling involves grinding, washing, melting, and reforming packaging which removes some contaminants that absorbed into the polymer matrix during product use [5, 6].
Ideally, post-consumer waste should be sorted by polymer type and packaging sector, as an additive that is not approved for direct food-contact could become incorporated into a package that is in direct contact with food. This, however, is difficult to achieve due to the increase in curbside reclamation programs and the increasing use of common polymers, such as PET (used for beverage bottles and food packaging) for non-food applications (cleaners, personal care) [5]. Poor sorting can result in the incorporation of non-food-contact polymers into the recycling feed-stock for direct food-contact packaging. Although the FDA believes that acute consumer exposure to chemical contaminants from plastic food containers produced via secondary and tertiary recycling is low (due to low initial concentrations within the materials), trace amounts of toxic compounds have the potential to migrate into food items [5, 8]. As a result, the FDA recommends that worst-case contamination assumptions be made for non-food-contact packaging that enters the recycling stream due to the increasing probability that recycling feed-stock can be comprised of 100% non-food containers [5].
The FDA believes that secondary recycling processes will not remove all unapproved additives (colors, antioxidants, and other additives with relatively high molecular weights) because such compounds are incorporated into the polymer matrix during fabrication [5, 10, 11]. Other plastic components with lower molecular weights, such as plasticizers, oligomers, and monomers, have a much higher potential to migrate into food and can comprise up to 20% or more of a polymer’s mass [7, 8, 11]. In food-grade packages, the lipophilic nature of ester plasticizers favors their migration into oily and fatty food components [10]. The adverse effects of some plasticizers to human health are well known and can include negative effects on the reproductive and endocrine systems as well as respiratory and dermatological problems [10].

Contaminants from consumer use, such as cleaning solutions and brake fluid, are typically removed during the secondary recycling process as these contaminants are superficially sorbed into a container’s surface [5]. Even though the FDA believes that contaminants from consumer use will likely be removed during the recycling process, it is still recommended that recyclers incorporating non-food, post-consumer containers as feedstock establish that contaminant concentrations in received flake are less than the acceptable values empirically determined by the FDA [5].
The FDA mandates that manufacturers of food-contact packaging made from recycled plastic are responsible for ensuring that their products meet current specifications for similar packaging comprised of virgin material [5]. Recyclers must demonstrate that contamination levels in the packaging components are sufficiently low enough to comply with the Code of Federal Regulations (CFR) and FDA [1, 5]. The FDA believes that an Estimated Daily Intake (EDI) of a contaminant lower than 1.5 micrograms/person/day (0.5 ppb dietary concentration) would be considered acceptable as contaminant concentrations lower than the EDI are considered to be of negligible risk [2-5, 7].
The EDI of a substance is dependent on the amount of migration into food and the percentage of the daily diet that is expected to be consumed via each type of packaging. The consumption factor (CF), expected exposure of indirect additives to food, is based on historical and projected data for national food packaging [2-4]. The CF, in conjunction with food packaging distribution factors (differentiated by packaging type) (fT), are calculated based on the fraction of total food that contacts aqueous, acidic, alcoholic, and fatty substances. Separation of food packaging by composition and product application is necessary as the amount of contaminant and additive migration is partially dependant on solubility within the food product [2-4].
The projected concentration of an additive in each food type is determined by multiplying individual fT values by the amount of migration measured in a food stimulant [3, 4]. A weighted migration is calculated by adding the migration level from each individual simulant type. The weighted migration is then multiplied by the CF to yield the total migrant concentration in the diet. Assuming a 3000 gram per day per person intake (both solid and liquid), the migrant concentration is converted to an EDI [3, 4]. The migrant EDI must be less than the migrant acceptable daily intake (ADI) if it is to be allowed in food packaging fabrication [2, 3]. The ADI values are determined by multiplying zero-effect levels from animal feeding studies by a safety factor [3, 7].
In cases where post-consumer polymer is expected to be blended with virgin polymer, the maximum acceptable contaminant level is calculated using the FDA’s recommended approach and is divided by the fraction of post-consumer-recycled content [5]. The validity of the FDA’s safety evaluation strongly depends on the ability of extraction methods to model actual packaging situations, and the accuracy of the animal feeding studies [3].
The main objective of this study was to assess total extractives compliance (Code of Federal Regulations 21CFR177.1630) of domestic, industrially-manufactured polyethylene terephthalate rigid containers containing 0, 70, or 100% post-consumer content with intended use for fresh-cut produce applications. As the results obtained from utilizing the 21CFR177.1630 procedure are non-specific, a secondary objective was to characterize the food simulants which had been exposed to the rigid container samples for potential migrants to food. This was accomplished qualitatively using gas chromatography-mass spectroscopy.
Methods and Materials
Domestic thermoformed polyethylene terephthalate (PET) rigid containers with label claims of 0, 70, or 100% post-consumer (PC) recycled water bottle content were collected from retail stores. The food simulants specified by 21CFR177.1630 and used in this study were n-heptane, 8% ethanol in water (v/v), and water [1]. N-heptane was used as received from the manufacturer. Deionized water (16.7 mega-ohm) was produced using a Barnstead Nanopure II water purification system. A 95% ethanol solution was diluted to 8% (v/v) with nanopure deionized water.
Preparation of specimens
The experimental design was a completely randomized 3 x 3 factorial with 3 specimens per treatment combination. A circular disk was cut from each package slightly larger than the area of exposure to ensure a good seal between the specimen and the analysis apparatus: the area of exposure to the food simulants was 6.61 in2 for each specimen. Disks were conditioned according to ASTM D618-08 [12] using a Thermo-Forma Scientific environmental chamber coupled to Watlow 982 series controllers. Conditioning continued until the mass of each disk stabilized to within ± 0.1 mg for three consecutive measurements (the masses were recorded approximately every twenty-four hours). The mass of each disk was determined using a Mettler Toledo Model AB104 scale with a resolution of ± 0.1 mg.

Chemical Migration Analyses
Each specimen was analyzed for chemical migration according to Title 21, Chapter 1, Subchapter B, Part 177.1630 of the Code of Federal Regulations [1]. The 21CFR177.1630 states that each package must not desorb more than 0.5 mg of total chemicals per square inch into food simulants. The specified food simulants were nanopure deionized water, an 8% ethanol solution in nanopure deionized water, and n-heptane.
Specimens were tested using common glass Mason jars. Polytetrafluoroethylene tape was placed around the mouth and over the lip of each jar. Each jar was filled with 100 mL of the corresponding food simulant and specimens were placed on the PTFE-lined jar lips such that the food contact side of each specimen would be exposed to the food simulant once the jars were inverted. The specimens were then secured in place with metal locking rings.
To test for total migration, the jars were inverted and placed in an oven at 49 oC for 24 hours. After 24 hours, the specimens were removed from each jar, wiped clean, then placed in an environmental chamber for conditioning according to ASTM D618-08.
Gas Chromatography-Mass Spectroscopy
Each food simulant from the extractables testing was injected into a Perkin Elmer Clarus 600 GC equipped with a 0.25 mm I.D., 30 m Restek RTX 502.2 capillary column attached to a Perkin Elmer Clarus 600C mass spectrometer (MS). The carrier gas was hydrogen set at a constant flow rate of 2.5 mL/min with an inlet port temperature of 280 oC. The oven temperature ramping protocol was as follows: initial temperature 35oC for 5 min then increasing to 150 oC at a rate of 30 oC/min then increasing to 250 oC at a rate of 20 oC/min. The final temperature of 250 oC was held for 10 min. The MS was set to continuous scan mode at a rate of 5 scans/sec between m/z ratios of 35 and 300. Aliquots of pure solvent were analyzed by GC-MS to eliminate peaks associated with the food simulants.


Chemical Migration per 21 CFR177.1630
All three rigid container types with label claims of 0, 70, or 100% post-consumer recycled PET complied with the extractables limit for food packaging applications below 120 °F specified in 21CFR177.1630 (Table 1). The rigid containers consisting of 100% post-consumer-based PET exhibited the largest total migration which could be expected since the material feedstock source and composition were unknown. For all packages tested, the largest measured extractables occurred during exposure to n-heptane (Table 1).
Although the specimens were conditioned according to ASTM D618, it is apparent that the conditioning was insufficient to account for the hygroscopic properties of PET indicated by the negative migration from specimens exposed to food simulants that contain water (Table 1). Though some specimens absorbed ambient moisture, and likely water from the food simulants, the mass loss from all samples, including samples exposed to n-heptane, the most aggressive solvent, was sufficiently low that all rigid containers complied with with the extractables limit for food packaging applications below 120°F according to 21 CFR177.1630.
Total extractables testing according to 21 CFR177.1630 is non-specific which results in compounds that are generally regarded as safe (GRAS) to be considered as a part of the safety analysis. This can lead to “false positives” causing packaging to be labeled as “unsafe” when safety is not of concern. The non-specificity of 21 CFR177.1630 is also not useful to manufacturers as it does not indicate the source of contamination, i.e., whether it is the result of the manufacturers’ process or use of post-consumer feed-stock.
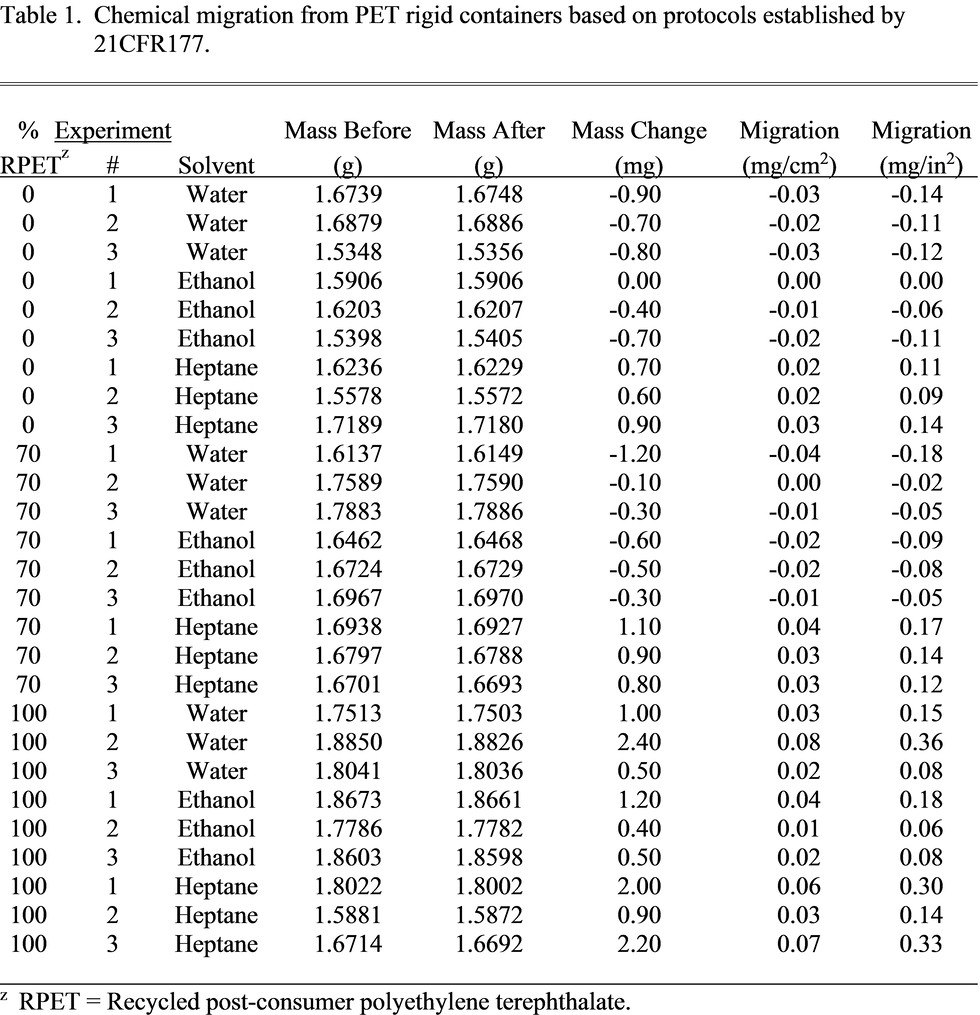
Solvents from the 21 CFR177.1630 extractables tests were characterized by gas chromatography-mass spectroscopy (GC-MS) for qualitative identification of potential migrants from food packaging into foodstuffs. It should be noted that peak integration was intentionally omitted due to the poor precision of the integration software and lack of ability to export the data into a program suitable for accurate and precise integration. The “Forward Fit” (Tables 2, 3, 4) indicates the probability that each mass spectrum at a specific retention time represents a pure sample (referenced by the MS National Institute of Standards and Technology (NIST) library entry). Peaks present in the sample’s mass spectrum, but not in the library mass spectrum, decrease the Forward Fit value; the same decrease in the Forward Fit applies to peaks that are in the library spectrum, but not in the sample’s spectrum. The “Reverse Fit” value (Tables 2, 3, 4) indicates the probability that the sample’s spectrum contains the MS NIST library entry, which can be useful when the sample’s spectrum contains multiple compounds. Peaks present in the library spectrum, but not in the sample’s spectrum decrease the Reverse Fit value. However, peaks that are present in the sample’s spectrum and not in the library spectrum have no effect on Reverse fit values.
In general, organic acids, aldehydes, chlorinated hydrocarbons, alcohols, esters, silanes, and siloxanes were present in the analyzed food simulants after exposure to samples (Tables 2, 3, 4). The molecular composition of compounds that desorbed from the rigid containers varied between food simulants. This was anticipated as desorbed compound solubility is highly dependent upon the molecular composition of the food simulant. Generally, the number of compounds that were identified by GC-MS from the PET containers increased as post-consumer content increased. This was expected as the composition of the post-consumer feed-stock is unknown and has a higher probability of containing contaminants from consumer use.
Water
The GC-MS analyses indicated that various compounds potentially into water-based foodstuffs from packaging comprised of virgin PET, post-consumer PET, and their blends (Table 2). 5-Chloro-1-pentene and cyano-acetic acid were observed to desorb from more than one rigid container type. This included the virgin PET rigid container, suggesting that the presence of these chemicals in the polymer matrix may be a result of the base polymer. 5-Chloro-1-pentene and other chlorinated hydrocarbons have been used as precursors to plastics, insecticides, herbicides, solvents, and pharmaceuticals.
Cyano-acetic acid is commonly used as a precursor to multiple-base polymer systems, surfactants, adhesives, agrochemicals and other non-plastic related compounds. Similarly, cyano-acetic acid was found as a migrant from only one virgin PET and one 100% post-consumer sample suggesting that its concentration within the PET matrix is low or that it has poor mobility within the polymer.
Oxirane-based compounds, which were only observed as migrating from rigid containers comprised of 100% post-consumer polymer, have acid-scavenging and plasticizing properties and were could have been used as an additive to hinder chain scission by residual acids formed from degradation by-products of contaminants (e.g. polyvinyl chloride and adhesives), and to replace phthalate-based plasticizers.
Allyl nonyl ester oxalic acid has been shown to have antimicrobial activity [13] and was found to desorb only from the 100% post-consumer rigid containers. Its presence could be from consumer abuse or post-consumer processing.
Other compounds detected from virgin rigid containers were 2-(aminooxy)-propanoic acid and 1-(ethenyloxy)-3-methyl-butane. Allyl sulfone, which can be used as a carbocation for important carbon-carbon bonding chemistry, and 3-ethyl-5-methylene-heptane, were measured to desorb from the 70% post-consumer-content rigid container.
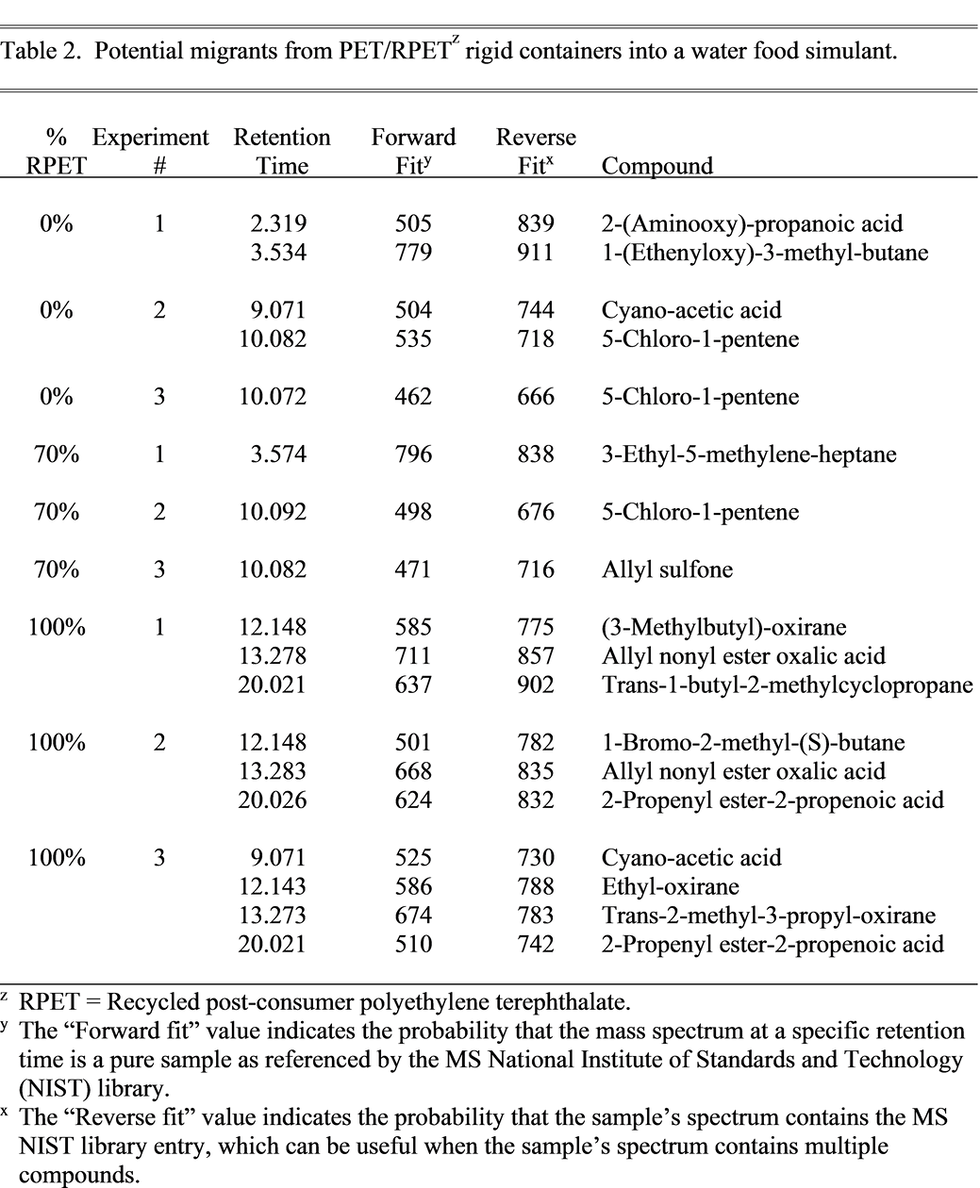
Ethanol
GC-MS analyses indicated that more compounds desorbed from each specimen into the ethanol solution with increasing post-consumer-material content in PET thermoformed rigid containers (Table 3). These results were supported the non-specific CFR results (Table 1). Cyano-acetic acid, also present in the water food simulant (Table 2), was found to desorb from every specimen independent of post-consumer-material concentration, further suggesting that its presence is due to the base polymer. Oxirane-based compounds were mainly present in specimens that contained 100% post-consumer content; however, they were also found to desorb from packages containing 70% RPET. 2-Propenyl ester 2-propenoic acid was observed as a migrant from all 100% post-consumer samples, whether 8% ethanol or water was used as the food simulant. When exposed to 8% ethanol, 1-nonamine was detected from only one of the virgin rigid containers while allyl sulfone was detected from only one specimen that contained 70% post-consumer material.

Heptane
GC-MS analyses identified more chemicals in the n-heptane food simulant from the rigid containers comprised of 100% virgin resin than from those containing 70% post-consumer content (4 vs. 3 compounds, on average, respectively; Table 4). However, the 100% post-consumer-content rigid containers, assumedly containing more compounds than the other two package types, had the most extractables content into n-heptane (7.3 compounds, on average). Thus, the overall trend was for more migration with increasing post-consumer content which was in agreement with results for migration into water and 8% ethanol.
Compounds such as 6-methyl-1-octene (typically found in coking petroleum residues [13]) and 1, 7-heptanediol were detected in all samples exposed to n-heptane, suggesting that the presence of these chemicals may be attributed to the base polymer. Other compounds from virgin resin-based packages included 3, 7-dimethyl-(S)-1-octanol (a common fragrance ingredient in shampoos, decorative cosmetics, toilet soaps, etc. [14]), octamethyl-cyclotetrasiloxane (a non-oily silicone fluid used primarily to make other silicone materials [15], likely a mold release), and trichlorodocosyl-silane.
All samples of 70% post-consumer PET released the same compounds into heptane -- 6-methyl-1-octene, 1,7-heptanediol, and trans-1-butyl-2-methylcyclopropane -- and all had strong correlations with the NIST library entries.
3-Methyl-1, 5-petanediol (a polyester plasticizer and precursor of polyester and polyurethane resins), (Z)-3-tetradecene, and bis (2-ethylhexyl) ester hexanedoic acid (a widely used plasticizer) were found in the heptane food simulant from all three 100% post-consumer PET packages. Allyl nonyl ester oxalic acid and 3,4-dimethyl-1-pentanol were detected from two of the three 100% post-consumer packages.
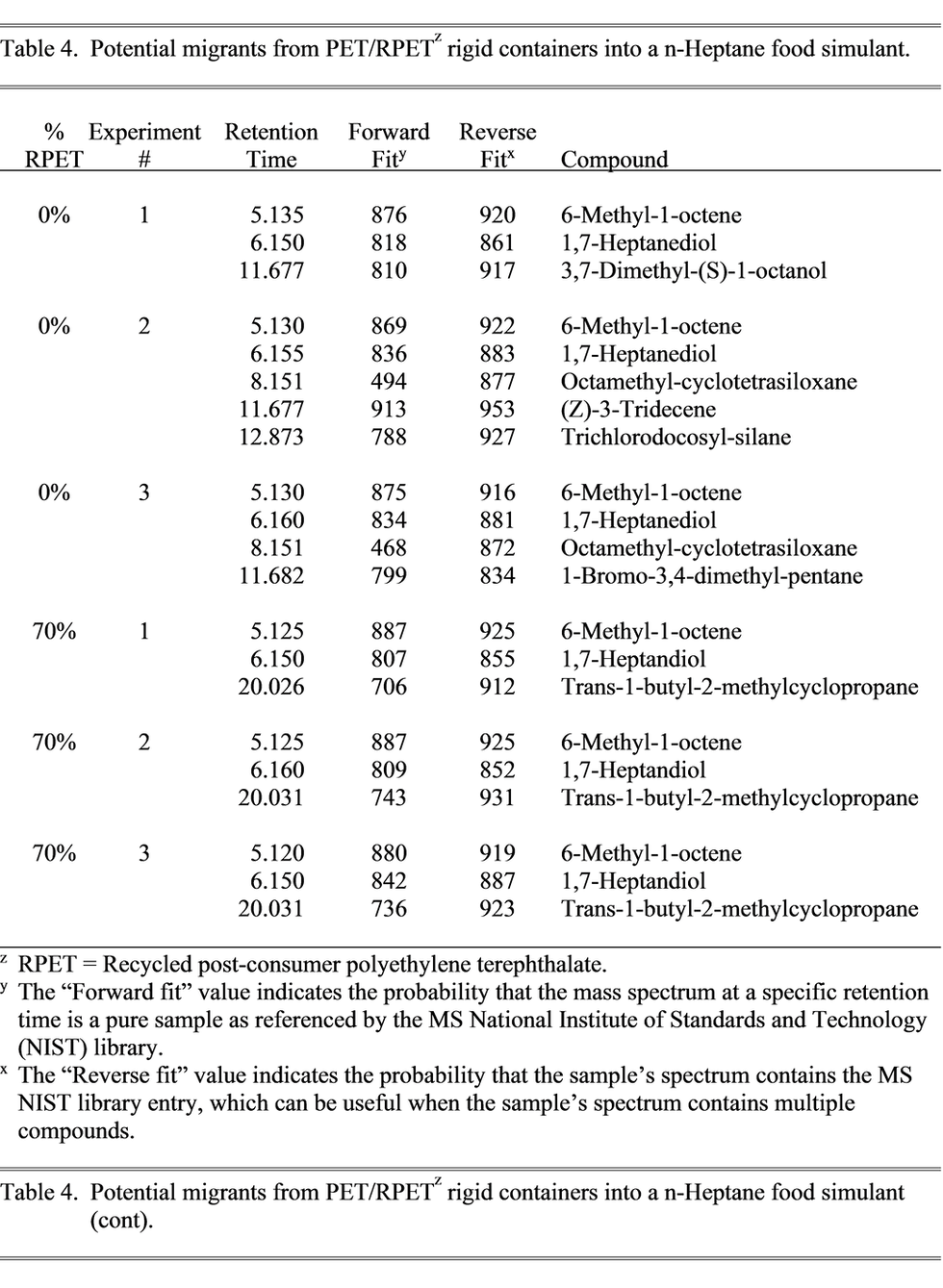
Conclusions
Three types of industrially-manufactured polyethylene terephthalate (PET) rigid containers with label claims of 0, 70, or 100% post-consumer (PC) content were tested for total extractable content according to the Code of Federal Regulations. The results of the CFR testing indicated that the three PET packages were acceptable as food packaging independent of post-consumer content for applications below 120 °F. The largest extractable content from the packaging into the food simulants occurred with the 100% PC material. This was anticipated as the potential for a package to contain a higher variety of compounds increases as post-consumer content increases.
The gas chromatography-mass spectroscopy (GC-MS) analyses of the food simulants indicated that CFR analysis can be misleading due to the hygroscopic properties of PET. The GC-MS analyses also indicated that more compounds are likely to migrate into fatty foods than alcoholic or water-based food items. However, it has been suggested that n-heptane may be too aggressive to be utilized for a food simulant for most polymers [3]. In general, organic acids, aldehydes, chlorinated hydrocarbons, alcohols, esters, silanes, and siloxanes were detected in the food simulants after CFR analysis.
This study determined that chemical migration increases as post-consumer recycled content increases in thermoformed PET rigid containers (confirmed by both CFR analysis and GCMS). Although the packages satisfied the Code of Federal Regulations, further analysis of the food simulants by gas chromatography-mass spectroscopy indicated that lower molecular weight organic acids, aldehydes, chlorinated hydrocarbons, alcohols, esters, silanes, and siloxanes potentially contaminate foodstuffs while packaged. As a result, PET packages containing post-consumer content should be continuously monitored for CFR compliance and food safety. Future research should include toxicological studies of identified compounds to assess the risks associated with using post-consumer feedstock for direct food contact packaging. Other research should include developing a total extractable analysis procedure that accounts for the hygroscopic properties of polyethylene terephthalate, while limiting exposure to only the food contact surface, to more accurately determine the mass of extractables from plastics into water-based simulants.
References
[1] Anonymous, Title 21, Chapter 1, Subchapter B, Part 177.1630 U.S., in, Government Printing Office, Washington D.C., 2014.
[2] Heckman, J.H., Food packaging regulation in the United States and the European Union, Regulatory Toxicology and Pharmacology, 2005 42 96-122 http://dx.doi.org/10.1016/j.yrtph.2005.02.002
[3] Schwartz, P.S., Food packaging regulation in the United States, Food Additives & Contaminants, 1988 5 537-541 10.1080/02652038809373687
[4] Van Der Heijden, K., S. Miller, International food safety handbook, CRC Publishing, Boca Raton, 1999.
[5] Anonymous, Guidance for industry: Use of recycled plastics in food packaging: Chemistry considerations, in, U.S. Dept. of Health and Human Services, FDA, Center for Food Safety and Applied Nutrition College Park, 2006.
[6] Franz, R., M. Huber, O.-G. Piringer, A.P. Damant, S.M. Jickells, L. Castle, Study of Functional Barrier Properties of Multilayer Recycled Poly(ethylene terephthalate) Bottles for Soft Drinks, Journal of Agricultural and Food Chemistry, 1996 44 892-897 10.1021/jf950419m
[7] Piringer, O., R. Franz, M. Huber, T.H. Begley, T.P. Mcneal, Migration from Food Packaging Containing a Functional Barrier: Mathematical and Experimental Evaluation, Journal of Agricultural and Food Chemistry, 1998 46 1532-1538 10.1021/jf970771v
[8] Schmid, P., M. Kohler, R. Meierhofer, S. Luzi, M. Wegelin, Does the reuse of PET bottles during solar water disinfection pose a health risk due to the migration of plasticisers and other chemicals into the water?, Water Research, 2008 42 5054-5060 http://dx.doi.org/10.1016/j.watres.2008.09.025
[9] J. Vandenburg, H., A. A. Clifford, K. D. Bartle, R. E. Carlson, J. Carroll, I. D. Newton, A simple solvent selection method for accelerated solvent extraction of additives from polymers, Analyst, 1999 124 1707-1710 10.1039/a904631c
[10] Bonini, M., E. Errani, G. Zerbinati, E. Ferri, S. Girotti, Extraction and gas chromatographic evaluation of plasticizers content in food packaging films, Microchemical Journal, 2008 90 31-36 http://dx.doi.org/10.1016/j.microc.2008.03.002
[11] Silva, A.S., R.S. García, I. Cooper, R. Franz, P.P. Losada, Compilation of analytical methods and guidelines for the determination of selected model migrants from plastic packaging, Trends in Food Science & Technology, 2006 17 535-546 http://dx.doi.org/10.1016/j.tifs.2006.04.009
[12] International, A., Standard Practice for Conditioning Plastics for Testing, in: ASTM D618-13, ASTM International, 2013.
[13] Selvin, J., S. Shanmughapriya, R. Gandhimathi, G. Seghal Kiran, T. Rajeetha Ravji, K. Natarajaseenivasan, T.A. Hema, Optimization and production of novel antimicrobial agents from sponge associated marine actinomycetes Nocardiopsis dassonvillei MAD08, Applied Microbiology and Biotechnology, 2009 83 435 10.1007/s00253-009-1878-y
[14] Lapczynski, A., S.P. Bhatia, C.S. Letizia, A.M. Api, Fragrance material review on 3,7-dimethyl-1-octanol, Food and Chemical Toxicology, 2008 46 S139-S141 https://doi.org/10.1016/j.fct.2008.06.023
[15] Burns-Naas, L.A., R.G. Meeks, G.B. Kolesar, R.W. Mast, M.R. Elwell, J.F. Hardisty, P. Thevenaz, Inhalation Toxicology of Octamethylcyclotetrasiloxane (D4) Following a 3-Month Nose-Only Exposure in Fischer 344 Rats, International Journal of Toxicology, 2002 21 39-53 10.1080/10915810252826000
Contributors
Greg Curtzwiler1, Keith Vorst1*, and Wyatt Brown1,2
1 Polymer and Food Protection Consortium, Department of Food Science and Human Nutrition, Iowa State University.
2 Horticulture and Crop Science Department, California Polytechnic State University
To find out more or learn about the authors please visit their contributor pages here: