Concept of Permeation and Barrier Materials
- Georgia Gu, Sr. Global Applications Specialist
- Oct 5, 2017
- 4 min read
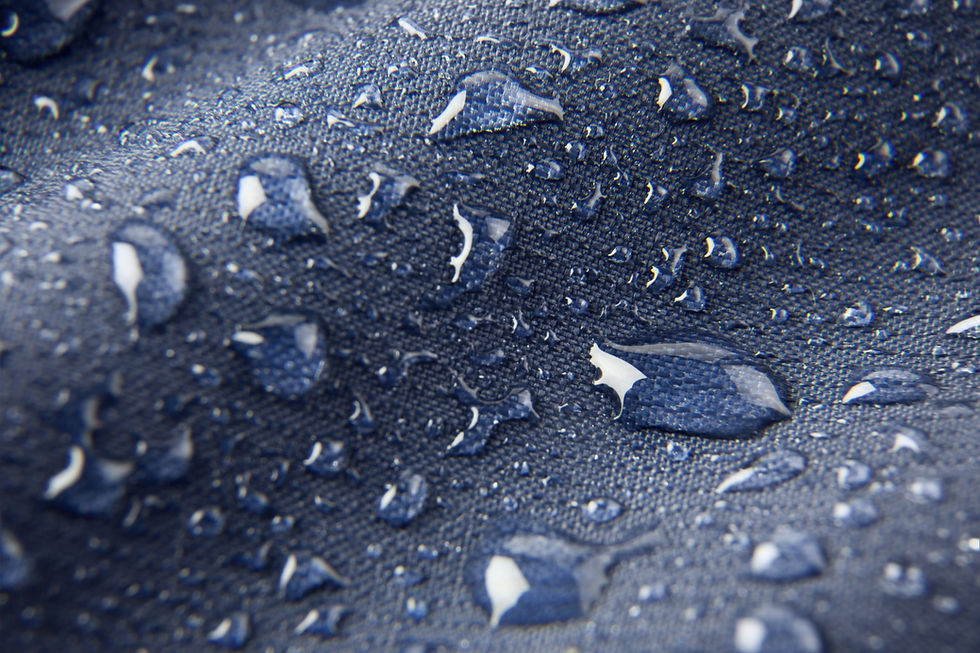
Why Packaging?
Modern Packaging has the following basic functions:
Containment - It should have proper size and shape, be easy to use
Protection - It should provide proper barrier that product can meet the desired shelf life. Also it should have proper physical strength that can withstand transportation
Information - Ingredients and nutrition of the product should printed on the package
Marketing - Designed to have special appearance to attract consumers
With the advancement of modern science and technologies, packaging materials have greatly evolved from traditional to modern time. Examples of traditional packaging materials are glass bottles, metal cans and paper bags. Examples of modern packaging materials are polymer bags or bottles and packages with multi-layered materials.
For traditional packaging materials, they are either non-permeable such as glass and metal, or highly permeable such as paper. For the non-permeable packages, the possible leak paths such as seams, closure interface are of the most concern. For modern packaging materials that are mainly polymer or composite materials, permeation of the material itself should be considered, in addition to possible leak paths of seams, closure interface, etc. Please remember that all plastics are permeable. It is impossible to study the barrier property of a packaging material without studying the permeation of the material.
What is Permeation?
Permeation is a process that is invisible but happens all the time. Look at the typical PET bottle that is filled with carbonated soft drink (Figure 1). Since the CO2 pressure inside the bottle (usually 4atm to start with) is higher than the ambient CO2 pressure, the partial pressure difference makes CO2 permeation happen from inside the bottle towards outside exterior environment. On the other hand, the ambient air (21% oxygen) permeates into the bottle at the same time.

Permeation rates determine how much barrier or protection is provided from packaging materials. The lower the permeation, the better the barrier. Here, the protection means to prevent the failure of a product due to the quality change.
For example, in the food industry, products basically have the following failure modes:
• Rancidity
– Oxidation of unsaturated fats and oils
– UV induced oxidation
• Stale
– Moisture gain
• Dehydration
– Moisture loss
• Flavor loss or off-flavor
– Scalping, migration
In order to protect the product from failure within the desired shelf life, proper barrier properties are required for different products:
• Gas Barrier
– Oxygen
– Carbon Dioxide
• Light Barrier
– Visible
– Ultraviolet
• Moisture Barrier
• Aroma and Flavor Barrier (chemical barrier)
Permeation Basics
Permeation follows Solution-Diffusion Mechanism. The gas absorbs at the entering face and dissolves within the material at the high-pressure side of the material, diffuses through the polymer phase, and desorbs or evaporates at the low-pressure side (Figure 2).

Figure 2: Solution-Diffusion Mechanism Diagram
Permeation can be expressed as:
Permeation rate:
cc(STP) * mil / (100in2 * day * atm)
cc(STP) * cm / (m2 * day * atm)
cc(STP) * cm / (cm2 * sec * cmHg)
Transmission rate:
cc(STP) / (100in2 * day)
cc(STP) / (m2 * day)
The barrier property of a polymer material is impacted by the environment, e.g., temperature, relative humidity) and Fickian behavior of the material itself.
Permeation rates typically change 5-7% per degree C (Figure 3).
Crucial errors can occur when testing at elevated temperatures close to the glass transition temperature (Tg) of the sample (Figure 4).
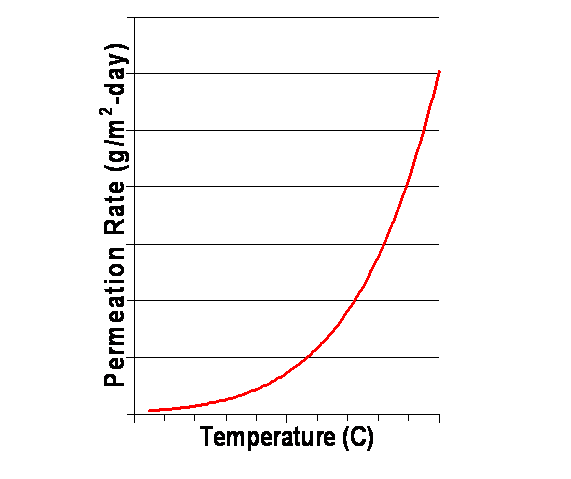
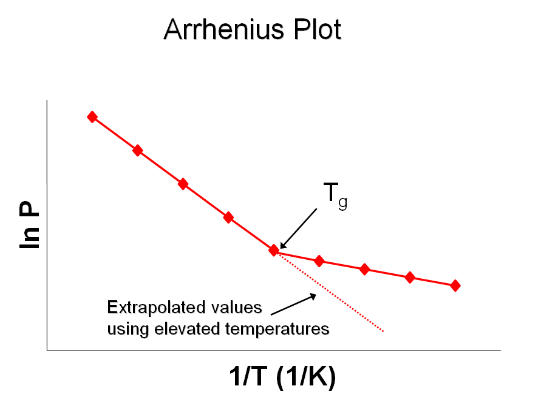
Figure 3: Permeation and Temperature Figure 4: Tg on Arrhenius Plot
RH can greatly affect permeation for hydrophilic materials. Proper RH generation and measurement are necessary for accurate permeation results. Figure 5 shows how RH affects OTR of different materials.

Figure 5: RH affects OTR of the EVOH film
For Fickian materials (or those that obey Fick’s Law), permeation is linear with concentration for all concentration ranges. Non-Fickian behavior results from changes in materials due to polymer and permeant interactions (e.g., swelling, plasticizing). Displayed graphically, Fickian and Non-Fickian materials would look like the following (Figure 6):

Figure 6: Fickian vs. Non- Fickian Behavior
Case Study: Selecting Packaging Barrier Materials Wisely - Using Destination Environment Conditions
The ultimate goal of packaging is to provide a sufficient barrier tfor the product to maintain its quality within the desired shelf life. However, the expense of over-packaging is to be avoid. In order to select packaging materials wisely, one should combine technical, geographical and economical knowledge.
Following is an example of how to select packaging material for a snack product using destination environment conditions. The company produces waffle products which are exported to three different global regions. Due to the different environmental conditions in each region, different grades of packaging materials should be chosen to achieve the desired shelf life.
Three grades of film materials were tested at three test conditions that mimic the environment of these three regions.
Table 7. Candidate film testing conditions and results
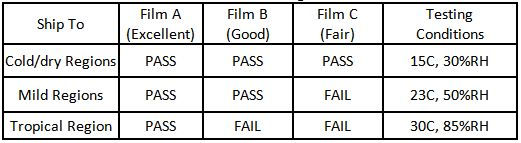
Results in Table 7 showed that Film A is the only choice for Tropical Region due to its high temperature and humidity condition. For the other two regions, more than one film could be chosen. Ask management for their input from marketing and economic points of view, and then decide whether the highest barrier should be used or if lesser barrier is sufficient.
The important of studying the barrier properties when selecting packaging material is evident. In order to evaluate the barrier properties of packaging materials, high quality permeation test instruments are required. Click Here to explore a variety of permeation instruments that can evaluate your barrier materials for your packaging applications.
Georgia Gu is Applications Specialist at AMETEK MOCON. You may reach her at georgia.gu@mocon.com or visit her contributor page.
Comments